A Gour Gopal Roy b Maha Nand Jha c Martin Mascarenhas c Sushanta Kumar Panda a. The wrinkling defects are a kind of buckling of the undrawn part of the blank.
Defects In Deep Drawing And Their Remedies
Shankar Kumar PGWLF1850156 8 9.
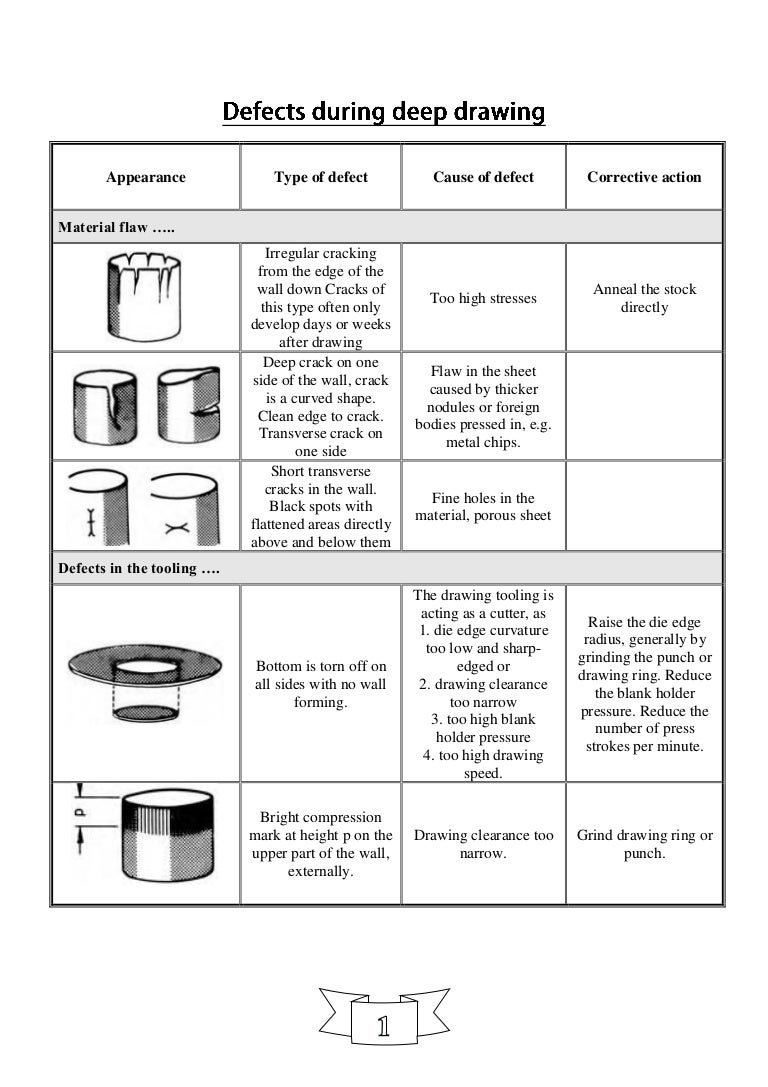
. Sipxmach is a deep draw metal stamping leading manufacturer for the aerospace communications industrial lighting medical military and furniture sectors. Most common defects occurred during this process are wrinkle and tear. What is the Defects In Deep Drawing Manufacturing.
Tearing is one of the most common defects. Excessive thinning in areas of the sheet metal is also an unwanted defect. Earing is one of the major defects observed in a deep drawing process due to the anisotropic nature of the sheet material.
The stress in the flange region during the deep drawing process is a combination of radial tensile drawing stress and a tangential compressive stress hoop. Failure of sheet metal parts during deep drawing processes usually takes place in the form of wrinkling or tearing. Defects In Deep Drawing And Their Remedies R Stretch Strains Yield point elongation.
Potential causes and remedies are also provided. 195-211 1981 0020-740381J040195-17502000 Printed in Great Britain. It is the Lagrange strain tensor component formation of a wavy edge on the top of a drawn cup that dλ Scalar necessitates extensive trimming to produce a uniform ν Poissons ratio top.
Deep drawn low carbon steel. The most common defects in deep drawing operations are wrinkling galling orange peeling earing and tearing. Deep drawn stainless steel.
Knowledge about the ear formation in deep drawing allows a prior modification of the process. Metal fractures very early in the. It does not provide on punch because friction between punch and blank improves draw ability by reduce tensile stress.
One of the primary defects that occurs in deep drawing operations is the wrinkling of sheet metal material generally in the wall or flange of the part. This is one of the most common deep draw problems. Steel material must be consumed within the strain aging time of material.
Our expert engineers prepare each metal punching blank in advance of the deep drawing process to ensure that the results are free from tears and other defects. We have been in the forming simulation business for over a decade. Lubrication lowers the forces increases draw ability and reduces defect in the part and wear on the tooling.
Defects in Deep-Drawn Parts. - deep drawn stamping parts. The following is a brief description of commonly found defects.
Due to improper clearance and punch force defect was occurred in drawing components. Reducin g the grain s ize prior t o drawing e ither by heat treatment or by adding grain refining the grains. Develop defects if the process parameters are not selected properly.
Their occurrence is related to numerous factors such as blank hardness lubrication system quality of the die surface grain size and anisotropy of the drawn material holding down pressure and clearance between the punch and die. Mostly used lubricants in deep drawing process are mineral oils soap solutions and heavy duty emulsions. The description of such defects is discussed below.
Defects and Remedies in Stamping of Advanced High Strength Journal of Modern Mechanical Engineering and Technology 2014 Vol. Earing is a result of non-uniform flow of material into the die cavity from different anisotropy directions of the sheet. Defects in deep-drawn cylindrical cups.
Figure 12 shows the type of defects that may be found after drawing cups. Deep drawing mechanism parameters defects and recent results. Author links open overlay panel Anubhav Singh a Shamik Basak a Lin Prakash PS.
Up to 10 cash back The workpiece material used in a deep drawing process is anisotropic in nature due to a prior thermomechanical treatment. Therefore it is important to optimize the process parameters to avoid defects in the parts and to minimize production cost. The following metals are currently used to manufacture products through deep drawing Alloy Aluminum Brass Bronze Cold rolled steel Copper Invar Iron Kovar Molybdenum Nickel Silver Stainless steel Tungsten 19.
The flange of the blank undergoes radial drawing stress and tangential compressive stress during the stamping process which sometimes results in wrinkles. Identifying and Resolving the Most Common Defects in Sheet Metal Forming from StampingSimulation. Defects that occur during deep drawing of sheet metal can be controlled by careful regulation of process factors.
If this is too small too large or uneven the material can be cracked during drawing. The following is a list of common problems that may be encountered when deep drawing cyclindrical cups. Earing is one of the major t u0002ηij Non-linear part of incremental Green defects observed in the deep drawing process.
Our experience enables us to quickly and efficiently clear any roadblocks and provide you with sound and effective products and tools according to your specifications. Fracturing of the metal during the draw process can be caused by several issues although the most common is the clearance between the punch and the die. State of the art.
2 71 Over forming is a known solution for springback Splitting tearing is another defect type present in which is based on providing compensation in the the forming of AHSS from necking that starts from. Scratches Heavy scratches over the drawn cup may appear due to appearance of yield point phenomenon in the material. Many variables affect the failure these.
In the deep drawing process earing is one of the most common defects that occur 22 23 where non-uniform elongation in the radial direction as a result of anisotropy of the workpiece causes a. Shankar Kumar PGWLF1850156 7 8. Additional deep drawn metal.
Grain structure should be refined before deep drawing. Defects in Deep Drawing process. In this experiment both steel and copper were taken as a base material and deep drawing process was finished with different parameters and defect was analysed.
A major defect which affects the quality of the deep drawn cups is the occurrence of a wavy edge at the top commonly referred to as the earing defect. Prediction of earing defect and deep drawing behavior of commercially pure titanium sheets using CPB06 anisotropy yield theory. This defect is caused by the excessive compressive stresses if the slenderness ratio is higher than a certain value.
WRINKLES Wrinkles - caused due to excessive clearance between the punch and die. A number of defects may occur in deep-drawn parts.
Defects In Deep Drawing And Their Remedies
All Defect Of Deep Drawing Process
Defects In Deep Drawing And Their Remedies
Pdf Deep Drawing Mechanism Parameters Defects And Recent Results State Of The Art
Defects In Deep Drawing And Their Remedies
Defects In Deep Drawing And Their Remedies
Pdf Prediction Of Forming Defects In Deep Drawing Process By Finite Element Simulation
0 komentar
Posting Komentar